The Ford Flathead Engine 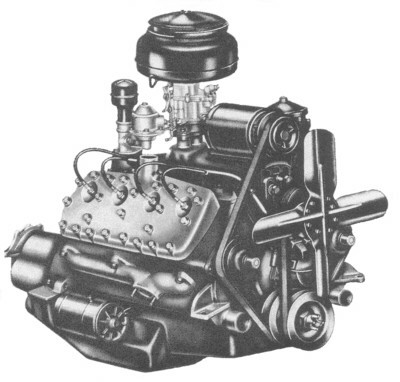
Project:
Flat-Head What It Takes to Succesfully Turbocharge a Flat-Head and Add Electronic Fuel Injection!!
Inter-Coolers Water To Air Air To Air Wastegate Valves Blow Off Valves Fuel Pressure Regulators Intake Manifolds Fuel Injectors Inter-Coolers Water To Air 


Above are pictures of the Water-To-Air Inter-Cooler we are going to use. it has a 3" inlet and outlet
fitting and will be placed after the initial Inter-Cooler which will be an Air-To-Air unit. One Air - Water Inter-cooler Core Size 10"x9"x4.5" Overall Size 18"x13"x4.5" Two 3" Air Inlet Outlet Two 0.7" Water Inlet Outlet 4.5"
Core This is a Huge Liquid to Air Inter-cooler, Perfect
for High Power Applications, Supports 1000+ HP
What do the Air to Water Inter-Coolers do?
The purpose of the Air to Water Inter-Cooler is to cool the Intake-Charge Air supply
as much as possible by using a large Aluminum Inter-Cooler that has cold water circulating through it. The Intake-Air Charge
is blown through the Inter-Cooler and the heat is absorbed by the cooled water that is circulating through the Aluminum structure.
The heated water, which is the by-product of cooling the Charged Air, is then pumped to a remote mounted Radiator (Cooler)
, where the heat is transferred to the Air as it passes through the Radiator (Cooler). The system needs to have a pressurized
Storage Tank, where make-up water is stored and replacement water can be added to the system. The system is Closed Loop, meaning
the water is constantly moving and circulating through the system, it's Radiators, Inter-Cooler and Hoses, as a self contained
system.
Items Needed for the Water - To - Air Inter-Coolers 1. Inter-coolers-1 2. 3" U-Bend Aluminum Tubing-1 3. 3" Silicone couplings-9 4.
3" 90° Aluminum Tubing-2 5. 3" Stright Aluminum Tubing-2 6. 3" T-Bolt Clamps-9 7. 3/4" NPT to An-8 Fittings-2 8. 3/8 x 1-1/2" SS Mounting Bolts -
4 9. 3/8"
SS Nuts - 4 10. 3/8" SS
Washers - 8 11. Water Pump 12volt -
1 12.An-8 SS Braided Hoses - 20' 13.An-8 straight Hose Fittings - 4 14. An-8 90° Hose Fittings-2 15. Make-up Water Canister 2 gal- 1 16.
1/2" to An-8 Stright Fittings-2 Air To Air Inter-Cooler
An Air to Air Inter-Cooler is
a system that relies on air movement through it's coils to remove the heat of the Charged Air that is flowing through
it's inside. We use the Air to Air Inter-Cooler as the
first line of defense in removing the heat associated with our Charged Air. Turbo-Chargers use Exhaust Gases to spin their
turbine/compressor, this extremely fast RP M's compress the incoming air and also heats it. Since heat is detrimental
to making horse-power, we need to filter out as much of the heat as possible. For this, we implore the use of Inter-Coolers,
in this case an Air to Air Inter-Cooler. The inter-Cooler in
positioned in the front of the vehicle so fresh air can pass through it's many fins, as the cool air passes through these
fins, the heat from the inside air is transferred to the fins and then to the passing cool air. This lowers the temperature
of the pressurized air inside the Inter-Cooler, and makes for a cooler, more dense air charge, which makes more power. In
our case, the cooled air that comes out of the Air to Air Inter-Cooler
is then routed to the Air to Water Inter-Cooler, where we again
Pass it through the Inter-Cooler with hopes of lowering it temperature. But instead of using air, we now use water to cool
the incoming air. After this, the cooler Charge Air is routed to the engine. 1. 2-1/2" T-Bolt Clamps - 10 2. 2-1/2" to 2" Reducers - 10 3. 2" Stright Aluminum Tubing-2 4.
2" 45° Aluminum Tubing-2 5. 3/8"
x 1-1/2" SS Mounting Bolts - 4 6.
3/8" SS Nuts - 4 7. 3/8"
SS Washers - 8 



Here in the above pictures you can see the Inter-Cooler we are going
to use on Project: Flathead. This unit is an Air-To-Air unit
that will take the out going air form the Turbo's and give it the initial cool down, then the air will go to the Air-To-Water Inter-Cooler where it will further reduce the Pressurized
Intake Air Temperature. This Inter-Cooler has a Inlet size of 2-1/2" for both Turbo's and an Outlet size of 3".
Blow-Off Valves 
Blow Off Valve (BOV) (a.k.a. Compressor Bypass Valve) What does it do: The purpose of a blow off valve or
compressor bypass valve is to prevent large pressure spikes
in the intake pipes when the throttle plate is closed while boosting, preventing the turbo from surging. The BOV sits between the turbo and the throttle body and has a vacuum line that is attached
to both the other side of the BOV valve and the intake manifold.
When you are boosting the pressure on both sides of the valve is essentially equal because the pressure in the intake manifold
is the same as in the intake pipes. When you close the throttle plate while boosting all that air slams into the plate and
pressure spikes. At the same time the intake manifold pressure drops to a vacuum, and thus so does the pressure on the other
side of the valve. The result is the valve opens wide to allow the pressure to vent out. Also included in a good BOV is some form of spring to aid in keeping the valve closed during modulating part
throttle situations so that the BOV doesn't open and cause
driveability problems.  

These are two (2) of the more popular styles of BOV Valve. The one on the bottom is very close to the style we will be using. When
selecting your BOV Valve, remember to take into account it's
mounting system and size, there are litterly dozens of different sized and mounts available. You only need pick one that is
right for your situation. The small picture is a 2-1/2" Aluminum pipe with the BOV Valve adapter welded to it, this adapter fits RS & S type BOV Valves. We
will use Two (2) Blow Off valves on Project:Flathead.
One will be mounted on each side, after the Charged Air leaves the Turbo-Charger and Before it Inters the Inter-Cooler.
Waste Gate Valve  
What does
a Waste-Gate
do ?A waste-gate is a valve that controls the exhaust flow to the turbo.
If the waste-gate is
closed, all of the exhaust gas goes to the turbo, spooling it up and creating boost. If the waste-gate valve is opened, exhaust gas coming
from the engine bypasses the turbo, therefore the turbo doesn't spin as much, and boost isn't created. The waste-gate regulates the amount of boost being
created by opening its valve and bypasses exhaust flow, when the given boost pressure signal is obtained Project:Flathead
will have two (2) External waste-gate's . Both will be mounted within close proximity to the Turbo-Chargers and will tie back into
the Exhaust System. |
Aluminum Piping 




The above is a good representation of what is
available in the form of Inter-Cooler Pipe Kits. We purchased a 2-1/2" and 3" Pipe kit for our project. The kits
on sites like E-bay are very competitive, in fact if you were to buy the same thing through a traditional site or parts house
that specialized in Turbo's you would pay 2 to 3 times as much. I found this to be true on everything associated with
Turbos! Be a smart shopper and get the most out of your money, it's just to had to come by.We purchased all our piping needs off E-Bay. They have an
incredible selection and the lowest prices around. like all shopping on the web, you have to be very careful about what you
buy and who you purchase it from. I like to stay away from those deals that just look too good to be true, and I also like
to stick with businesses that I have worked with before. If you find a new dealer that seams to have what you need at decent
prices, buy something small at first, and see how that purchase goes before you plunk down all of your hard earned cash for
the big ticket items.We have two (2) different piping systems. One is the system that comes straight from the Turbo Outlet. This system
is going to be plumbed in 2-1/2" Aluminum Polished Tubing, and will run from the Turbo-Charger to the Air-To-Air inter-Cooler.
The other system is the one the runs from the Air-To-Air Inter-Cooler to the Air-To-Water Inter-Cooler and then to the Engine.
This system will be plumbed in 3" Aluminum Polished Tubing. Both systems are of equal importance and both need to be
run with a host of important considerations. These considerations are, but not limited too, Engine Movement, Under hood clearance
issues, Aesthetics, Flow Considerations, Heat Soaking Issues, Ease of maintenance, and accessibility issues. If at all possible,
all tubing should be run in a manor that addresses the above issues. Your engine is going to move, it vibrates and rocks back
and forth as part of it's normal everyday routine. You must plan for that, along with the other issues discussed. When
possible, make every effort to allow normal maintenance type issues to remain UN-inhibited. Your car is going to need increased
oil changes, and other types of preventive maintenance, so keep these issues in mind when routing your tubing, and mounting
the Turbo-Chargers, or anything else associated with the system. There is definitely a huge difference between a well planed
Turbo installation and one that's not.
I Included these two (2) tech articles
from the Mega Squirt website. They are: "How to Fibricate an Intake manifold", and "How to Build a Fuel Rail". Both articles are excellent
reads on how you can take some of these "Technically Chalenged" Projects head-on and make it work. While our Project:Flat-Head will be a little different, there is still plenty
that can be taken from both of these fine articles. Also, anyone considering converting over to an EFI system, should first
consider looking at the Mega Squirt site, it's filled with loads of valuable information,
and they sell a great product at a very competitive price.How to Fabricate an Intake Manifold This article details the complete fabrication process on a custom intake manifold for a developmental
Mazda RX7. The basic design can be easily adapted for almost any engine design. Tools needed to fabricate this part would
include a drill press, lathe, bandsaw, hole saws, files and a TIG welder. This manifold was constructed from mild steel for
ease of assembly but it could also have been made from aluminum.Basic Design This plenum type design
uses a single throttle body attached to a plenum with separate intake runners for each port. Port type injectors are mounted
in each runner.
Head Flange The main flange which would be bolted to the cylinder head in the case of a piston engine, is made
from 1/4 inch steel plate to reduce warpage during welding. An intake manifold gasket can be used as a guide to trace the
flange outline and mark the port and bolt holes. The flange plate can be cut out using a bandsaw or plama arc torch. Bolt
holes can be drilled on a drill press. Intake runner tube holes can be done with a hole saw or plasma arc if they are not
round. Try to design the port holes so that the ID of the tubing used for the runners is the same of that for the finished
port size in your head. The runners should be spigotted inside the flange hole for ease of jigging.Intake Runners Runners are made from .050 to .065 tubing. Runner lengths can be adjusted within the space constraints to
help boost torque within the desired range. Short runners are good for high rpm torque as in a racing situation. Long runners
are more applicable for street use at lower rpms. For most street engines, try to keep the length from the end of the runner
to the valve at least 9 inches long and preferably longer. Available space usually limits this dimension when using straight
runners so curved runners using 90 degree mandrel bent tubing can sometimes be used to increase the runner length. As applied
to engines with oval or square ports, you will have to form the tubing into the port shape which is considerably more complicated.
Tubing should be cut off at precise lengths with a tubing cutter and carefully deburred. For maximum airflow, tapered runners
with velocity stacks inside the plenum can be made if you are capable of this type of work. This is very time consuming but
this design shows a 20-25% increase in flow over straight tubing runners.Plenum, End Plates
Depending on engine displacement and the throttle body used, the
intake plenum is usually constructed from .065 wall exhaust tubing in either 3 inch for engines under 1600cc or 4 inch for
most other engines. Holes must be cut in the plenum tubing with hole saws for the intake runner tubes and in the case of a
side mounted throttle body, for the throttle body tube also. The throttle body may also be placed on one end of the plenum
in place of an end plate, depending on component layout. Our RX7 manifold used 4 inch tubing. The plenum should be made at
least 2 inches longer than the dimension of the front to rear outside intake ports to allow better airflow into the outer
ports. Also plan for any vacuum taps for brake boosters or MAP sensors etc. at this point.End Plates, Throttle Body Plate End plates cap the plenum ends and are made from .050 to .065 plate stock. Cut them out with a bandsaw
or plasma arc. Make them about the same size as your plenum tubing OD. If you plan to put the throttle body on one end of
the plenum, this end cap will need to be made from 3/16 to 1/4 inch plate to allow for tapping of threads to hold the TB as
well as have a hole cut the size of the outlet TB bore. If the throttle body is to be mounted as in our RX7 manifold, use
1/4 plate for the TB flange. We like to tap right into the plate with fine threads for maximum strength.Throttle Body Throttle body choices are numerous. One should be selected which can flow the desired amount of air and fits
within the space limitations. Thought should be put into the ease of connecting either an air filter or turbo plumbing to
it. Too large of a throttle body for street use will often mean very sensitive "tip in" throttle response which
could be annoying. There is also no need of a 3.5 inch TB when your turbo plumbing is only 2.25 inches. Getting a throttle
body with a potentiometer type TPS already installed will save time and trouble. For many applications, the Ford 5L V8 and
4.6L DOHC throttle bodies work well. They are cheap, available and relatively compact. Ford Motorsport and Edelbrock make
larger sizes in 5mm increments. The 4.6L TBs are very compact and have a minimal amount of extra garbage on them. All Ford
TBs have potentiometer type TPSs also. Ford Explorer 4L throttle bodies can be ordered from your dealer. These are relatively
inexpensive and are 65mm with minimal garbage on the outside. Put some thought into a throttle linkage at this point also.
Injector Bosses
We usually make these out of 1 inch bar stock. We like to seal the
vacuum side of the injector with a 5/8 ID- 3/4 OD O-ring slid over the nose of the injector body. This will work on any standard
injector. You can pull off the stock O-ring and pintle cap. Bore the bar stock to .640-.650, straight through. This allows
a slight air gap between the boss and injector to reduce heat transfer and fuel boiling. A .740 counterbore, .040 deep is
machined at the end for O-ring retention and sealing. We usually cut off the bosses at 45 degrees so that they are about 1.35
to 1.5 inches long. This is a good entry angle for many injectors into the runner and is an easy angle to saw at.
Fuel Rail The fuel rail is usually made from 3/4 square tubing with a .050 to .065 wall. This shape allows
much easier drilling and jigging. 1/4 inch holes can be drilled at the port spacing interval. Over top of these holes will
be welded the upper O-ring bosses machined from 3/4 bar stock. These will usually be about 1/2 an inch long and have a .540
to .545 hole drilled for the O-ring to seal on. Carefully chamfer the entry side for easier O-ring fitment. End caps for the
rail are made from 1/4 plate and tapped for 1/8 NPT fittings. For a more detailed description on building a fuel rail, go
to the article on our tech page.Assembly
Once all of the pieces are cut out and deburred,
clamp the head flange to a scrap head if possible to reduce warpage. Carefully jig the plenum and runners to the flange and
measure for straightness. Tack weld the pieces lightly and re-check for straightness. You should still be able to move things
around a bit at this stage. Tack the opposite side of each joint and re-check again. Once you are satisfied, TIG weld all
of the joints. Weld on your end caps and TB flange. Let everything air cool. Now you must cut holes in the runners for
the injectors to poke through. Scribe a line across the runners where you want the center of the injectors to be. Now intersect
each mark on the runner with another line down the center of each tube. Punch mark and drill a 1/4 hole. Now drill straight
through with a 1/2 inch drill. Once you pierce the tubing, slowly lean the drill over at 45 degrees to oval the hole. The
injector bosses will be positioned over these oval holes so make sure before starting that you have enough room around the
boss to the flange that you will be able to get the welder in there. Assemble the injectors into the rail and slide the bosses
over the injectors. Carefully align the assembly so that the injectors are dead center through each injector hole in the runners.
Clamp in position and re-check. Lightly and quickly tack each boss in position. As soon as this is completed, either pull
the injectors out or water quench each tack to avoid heat damage to the injectors. Once you are satisfied that everything
is straight, finish welding the bosses without the injectors in place. Be aware that the bosses must be welded in very straight
and at the same depth for proper sealing.Finishing
You can weld on bolt down tabs on the fuel rail
and attachment points for the bolts on the manifold. A couple of long, 1/4 inch bolts usually suffice here. The manifold can
now be thoroughly cleaned with soap and hot water, then lacquer thinner. A good quality engine enamel can be used to finish
or better yet, get it powder coated.
Here are some photos of an intake manifold for
a Toyota 20R for more ideas:
 Note internal velocity stacks
Here
are a couple of manifolds modified to accept EFI type injectors through the use of weld-in bosses:
New injector bosses available with steel or aluminum bases, accepts 1/8NPT fuel fitting Curtesy of SFSEFI.com Great place for all your EFI questions!!
How
to Build a Fuel Rail This article is intended to guide
you through the process of fabricating a low-cost fuel rail for engines with a perpendicular injector mounting from scratch.
We will cover versions for both barb style injectors and domestic 14mm O-ring types. A sample O-ring style rail is shown here.
You will need access to a lathe, drill press, vise, calipers and welding equipment, preferably a TIG welder. We recommend
that the basic rail components be constructed from either mild steel or stainless steel rather than aluminum as steel gathers
far less heat after a hot shutdown leading to less fuel boiling in the rail. Precision is important here as misaligned bosses,
porous welds or wrongly dimensioned or finished pieces may lead to a fuel leak.Rail The main
rail piece can be fabricated from a piece of 3/4 inch square tubing with a .050 to .063 wall section. Square tubing makes
jigging other pieces far easier than round tubing. The rail must be long enough to span the distance between the injectors
on one cylinder bank. Add ½ inch to each end from the injector center lines to allow for welding of the boss and end
caps.Cut the tubing off straight with a hacksaw or bandsaw
and file finish the ends to remove burrs.Precisely measure
the distance between each injector on your intake manifold and write these dimensions down. Scribe a centerline mark on the
fuel rail from one end to the other and also scribe an intersecting line halfway down the rail. From this second mark, you
can transpose your injector spacing dimensions onto the rail, ensuring that the end locations are centered on the rail.You should measure again to be sure that you have accurately marked the proper
injector spacing. You can now punch mark these locations. Using a 1/8 drill bit in a drill press, drill through one side of
the tubing on your punch marks. Next, step up to 1/4 inch then drill to the final size of 5/16 inch. Radius the top edge with
a 3/8 bit and deburr the inside of the tubing with a long, slender file. Be sure to remove all burrs and carefully flush out
all filings.
O- Ring Bosses For injectors with 14mm domestic O-rings, use 3/4 inch round bar stock. Cut off the number of pieces
needed at around 9/16 inch lengths. Chuck these pieces in the lathe and face both ends until the total boss length is .450
inch. Center drill each boss, then use a 1/4 bit and finally a ½ inch bit to bring the boss ID out to .500 inch.Using a 3/16 or 1/4 inch tool, bore the boss ID in careful steps out to .540
to .545 inch. Chamfer both ends at 45 degrees to permit easy O-ring entry. The ID finish must be smooth to prevent fuel leakage
so use a fine feed and an ultra sharp tool here. If the finish is not perfect, you can carefully polish the ID with 400 grit
paper on a die grinder. Do not exceed .550 inch ID. O-ring crush must be .020 to .035 for proper sealing.
If you are building rails for use with 10 or 11mm O-ring injectors,
the same procedure as above can be used except the boss ID will be smaller. Carefully measure the injector O-ring OD without
crushing it with the calipers. Subtract .020 to .025 from this dimension. This is what you should bore the boss ID to.For injectors using an 8mm (5/16) barb connection, use an unplated 3/8 NF or
NC nut for the boss. Drill these out to 23/64 in the lathe and thread with a 1/8 NPT tap. You can then screw standard 1/8
NPT to 5/16 brass hose barb fittings into these which will fit the 5/16 ID hose used to connect to the injectors.
End Caps Rail end caps can be made from 3/16 to 1/4 plate stock. Finished dimensions should be 3/4 X 3/4 with
rounded corners to match the ends of the tubing. Drill an 11/32 inch hole, dead center in both caps and thread with a 1/8
NPT tap. These threaded holes will be used to mount the fuel inlet fitting on one end of the rail and the fuel pressure regulator
on the other end.
Mounting Tabs Mounting tabs to hold the rail to the intake manifold will vary widely depending upon the space limitations
and design of the manifold. We are showing a typical design with staggered tabs. These can be made from 1/8 plate stock. We
are using 4 inch long 1/4 NC bolts to hold down the assembly to the intake manifold. You will also have to weld some small,
threaded bosses to the manifold for the bolts to thread into.
Assembling the Pieces Center the O-ring bosses over the fuel holes drilled in the rail. Clamp in
position and tack. Weld all around, being sure that there are no pin holes. The next step is to weld the end caps in position.
Be sure to face the larger threaded end outwards for proper fitting engagement. Finally, the mounting tabs can be welded on
in the correct positions. Let the part air cool, then flush throughly with hot, soapy water and blow dry. If using mild steel,
rub the part down with lacquer thinner and paint with a high quality engine enamel. Light colors are a better choice as they
absorb less heat than black does for instance.The upper end
of the injector may either butt up against the rail itself or you may use C-clips fitted to the groove in the plastic upper
body to sit against the O-ring boss itself.
Injector Bosses on the Intake Manifold All Bosch style injectors use a lower body dimension of around .630 inch just
below the solenoid casing. The injector can be sealed to the intake manifold by sliding a 5/8 ID- 3/4 OD .065 section O-ring
over this area. The injector boss may then have a recess machined in its upper base .750 OD by .040 deep. This will capture
the O-ring to prevent it from squishing out.
Injector bosses can be made from either steel or aluminum 1 inch
round bar stock depending on the material used for the intake manifold. If you plan to seal the injector to the boss as described
above, bore the ID to around .645 inches. This will prevent metal to metal contact and reduce heat transfer and fuel boiling
in the injector. Counter bore the O-ring capture as described above. The boss can be cut off at any angle required for proper
mounting to the intake runners, 45 degrees is common.To use
the 14mm O-ring which is already in place to seal the injector, you will need to step bore the injector boss inside. Use the
same .540 to .545 ID as was used on the O-ring bosses for the fuel rails in the lower end of the injector boss. The upper
end of the boss can be bored to .645 for injector body clearance and the same O-ring can be slid over the body to provide
a crush zone for better sealing and less heat transfer.Injector
depth is critical. It is important to ensure that the fuel spray does not impinge on the injector boss wall before entering
the intake runner. It is generally OK to have the end of the pintle up to 1/4 inch recessed inside the boss from the runner
wall to 3/8 inch projecting into the airstream.When using gasoline
as fuel, the injector can be placed from 1 to 4 inches from the port. When using alcohol, the injector should be placed further
from the port to aid mixing. This will often increase power while hurting emissions slightly.The injector bosses on O-ring style injectors must be precisely placed for depth and
angle to ensure proper fit and sealing. This should be repeatedly checked using the whole rail with injectors pressed
in. Clamp the bosses in place before welding.Curtesy
of SFSEFI.com Great place for all your EFI questions!! Project:Flat-Head... Our Intake Manifold We are going to Hand Fabricate our own
Intake Manifold and Fuel Rail!! This is a huge step and will require many man hours for the build as well as more money then
originally planed for. The plan was to re-use the original intake manifold and modify it to work with a mass air flow sensor
and individual fuel injectors, but it wasn't feasable. It would have been possible to use a aftermarket intake manifold
that was set-up for a 4-barrel carbuator, and then run a throtle-body type injection set-up. This would be fairly simple and
would work well under most conditions, but I am looking for more horse-power and Direct Port Injection. In my search for the right parts and pieces to build our Intake
Manifold and Fuel Rails, I found there were many that offered some parts and pieces but very few that offered everything one
might need to build a complete Manifold or Fuel Rail. One Store that was an exception to the rule was, Ross Machine Racing.
They not only had everything I needed, but they had top of the line, quality, products that would work very nicely for Project:Flat-Head,
or any other project from restoration to full on Drag Racer. I
took a very long time thinking about the desicion of weather I wanted to take this direction with Project-Flat-Head. This
was now getting very serious and the cost was rising faster then I wanted. What was originally suppose to be a simple but
modern version of a Flat-Head, has now turned into a full blown race enigne with state-of -the-art Fuel Injection and Twin-Turbos.
I don't know how I got to this point, but I do know that their is only one real way to go, and that is to go all the way
now. So, with that thought, I sat down and ordered everything needed for the Intake and Fuel Rail systems. If this is suppose
to be an all out Flat-Head build-up then lets go for it! Ross Racing Machine 08-23-07 Today
we placed the order for most the parts needed to make our Intake Manifold and the Fuel Rails. The following is a copy of the
order placed. | Ross Machine Racing Internet Store | SHOPPING CART >>
BILLING/SHIPPING >> PAYMENT >>
CONFIRMATION >> RECEIPT
All orders are processed with SECURE SOCKETS LAYER TECHNOLOGY |
|
| Your shopping cart contains:
| | DELETE | | ITEM NUMBER | | ITEM NAME | | ITEM OPTIONS | | QTY | | PRICE | | SUBTOTAL | |
|
| 202702-6-6s | Dash 6 AN - Dash 6 O-ring Fitting (minimum order for fittings alone must total $20.00) |
| $3.50 | $17.50 | | | 900598-65
| Dash 6 O-ring Boss Plug (minimum order for fittings alone must total $20.00) | | $3.50 | $14.00 | | | 6401-6-4
| Dash 6 O-ring - 1/4" Male NPT Fitting |
| $3.50 | $14.00 | | | RMR-065
| Dash 6 High Spiral Tap | | $32.50 | $32.50 | | | RMR-064
| 14mm O-ring Fuel Injector Port Tool |
| $129.95 | $129.95 | | | RMR-033
| 4x4 Square Extrusion | | $29.95 | $59.90 | | | RMR-072
| 5 Inch Universal D Plenum | | $44.95 | $89.90 | | | RMR-048
| Universal Plenum Vacuum Endcap | | $29.00 | $29.00 | | | RMR-047-075
| 75mm Universal TB Plate | | $49.00 | $49.00 | | | RMR-0274
| 4 Fuel Injector Bungs | | $24.00 | $48.00 | | | RMR-019
| Dash 6 Fuel Rail Extrusion (2ft min) |
| $10.00 | $30.00 | | | RMR-050
| Universal Fuel Rail Clamp | | $15.00 | $60.00 | | | 1/2 x 4 6061-T6
AL | 1/2" x 4" 6061-T6 Flange Plate Material | | $12.00 | $24.00 | | Subtotal does not include tax and
shipping and handling rates, which will be calculated during check out. | SUBTOTAL
| $597.75 |
|
|
|
Lets look at just what we purchased and how it
will affect the build-up. 1. 202702-6-6s | | Dash 6 AN - Dash 6 O-ring Fitting |

202702-6-6s | | Dash 6 AN - Dash 6 O-ring Fitting |

This fitting will be used just like the pictures show, as the fuel feed and or
return fittings on the fuel rails. These are O-Ring type fittings and do a much better job of sealing then NPT or National
pipe threads do. There is no taper to the treads and less chance of cracking or leaking then the O-Ring type fittings. I suspect
these will one day replace the tappered type fittings. 2. 900598-65 | | Dash
6 O-ring Boss Plug |

These are also O-Ring type fittings and this one is just a plug, to seal off any un-needed
AN-6 thread. 3. 6401-6-4 | | Dash 6 O-ring - 1/4" Male NPT Fitting |
6401-6-4 | | Dash 6 O-ring - 1/4" Male NPT Fitting |

Again, these are AN-6 O-Ring type fittings, and these allow a connection between An-6
O-Ring threads and 1/4" NPT threads. 4. RMR-065 | | Dash 6 High Spiral Tap |
These is a special
Tap made just to cut An-6 O-Ring threads. I'm not sure how hard they are to come by, but I couldn't find another any
where! Maybe I'm not looking in the right places, but I normally can find just about anything I need. This Spiral Tap
is made for Aluminum and other light metals, the huge voids in the Tap, allow the removed metal room to move, and keep the
Tap from becoming clooged. At a little under $40.00 it's money very well spent, for this project and for all others too
follow.
5. RMR-064 | | 14mm O-ring
Fuel Injector Port Tool |

This and the tap might seem like over-kill for osme one the isn't into manufacturing
Fuel-Rails or Modifing Intake Manifolds, but your wrong. These two (2) tools will save me money, even if this is the only
time I use them (I sure hope not). Buy going ahead and purchaseing the Tap and Injector Tools I can Elliminate the normal
deal of sending by Fuel-Rails out for drilling and or machine work. The Injector Tool, does three seperate and very important
funtions. It drills a pilot hole in the fuel rail or intake Manifold, wich will go thru the Fuel Rail and be the path that
the Fuel follows to the Injector. Then it opens up the Fuel Rail to the exact size of the 14mm Fuel Injector, allowing it
to seat in the Fuel-Rail and still seal with it's O-Rings. And the last machining step is to slightly open the start of
the start of the fule injectors hole, so the O-Rings can easily slide over the aluminum edge. If I was to have this done locally,
it would cost way more then the tool cost alone. I would also have to make sure everything was set and ready to go, and all
the holes would have to be cut at the same time, no single cuts to make sure everything is right, and no experimenting. Yes
$140.00 is high, but it's also well spent, and I have the tool after I'm finished with this project for future projects
or to modify other peoples Fuel-Rails down the road. This and the Spiral Tap will be two tools I look forward to useing and
will gladly welcome into the fold of my present tool chest. 6. RMR-033 | | 4x4 Square Extrusion |

We will use this 4" x 4" Square Aluminum Tubing
as the base for our Intake-Manifold. It will be mounted flush to the Intake Manifold Plate, and will have to be machined so
the Intake runners can pass throuhg it.
7. RMR-072 
This D-Plintum Extrusion will be the upper portion
of our Intake manifold. This will be the piece where the 75mm Throttle Plate attaches to, and will give us the Intake Volume
we need. 8. RMR-048 
We will use this to enclose the rear of the D-Plentum. 9. RMR-047-075 
This adapter will be mounted in the very front of
the D-Plentum, and will accept the 75mm Ford Throttle body we have. This is also the same spot where the 3" Inter-Cooler
pipe will terminate. 10. RMR-0274 
These Bungs may or may not be needed, I got them
because I wn't know if there will be enough matterial on the Square Plentum to hold the fuel injectors in place. if not,
then we will use these and they will hold the bottom portion of each Fuel -Injector in place. 11.
RMR-019 
This is the An-6 Fuel Rails, we will machine our
own fuel injector holes, and will tap the AN-6 threads in each end 12. RMR-050 | | Universal Fuel Rail Clamp |

Four of these will hold each fuel rail in place. They are nicely made and will
do a fantastic job of securing each fuel rail so there wont be any leaks around any fuel injectors. 13.
1/2 x 4 6061-T6 AL These is just some extra 4" x 4" x 1/2" thick Aluminum I bought to
make the front and back plates for the 4" Square Plentum. I might also use some of it for brackets and or braces. | | 1/2" x 4" 6061-T6 Flange Plate Material |
| | Dash 6 Fuel Rail Extrusion (2ft min |
| | 4 Fuel Injector Bungs |
| | 75mm Universal TB Plate |
| | Universal Plenum Vacuum Endcap |
| 5 Inch Universal D Plenum |
|