The
Ford Flathead
Engine
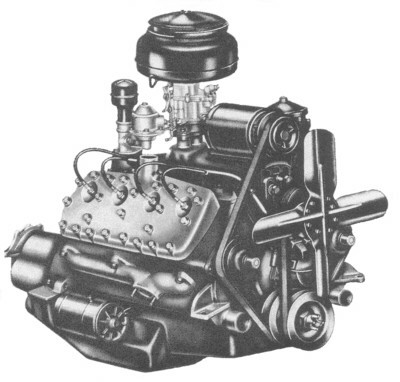
Fabricating the
Parts & Putting It All Together
Making the Headers
Fabricating a
Turbo Header
This article details the process of fabricating a low cost turbo header.
The subject engine is a Toyota 22RE engine using a Garrett T4/T3 hybrid turbo.
Flanges
The head and turbo flanges are laid
out on 3/8 to 1/2 inch mild steel plates using the gaskets as tracing patterns. A drill press and hole saw are used to cut
the holes. For rectangular holes, 4 smaller holes may have to be drilled and then hand filed to obtain the correct shape.
If you have access to a plasma arc cutter, this job will go much faster!
Tubes
This header was constructed from 1 1/4 schedule 40 NSP weld els and tubing. The els are available from most industrial plumbing
and gas fitting shops and are very inexpensive. They are made from a high strength, weldable alloy steel and have a nice V
at each end to pour in a good, strong weld. They are available in 45 and 90 degree bends and short and standard radius styles.
We recommend using the standard, longer radius ones whenever possible as they have less flow restriction. The els are also
available in different IDs. The size describes the approximate ID, not the OD. The 1 1/4 ones are actually about 1 3/8 ID.
Straight schedule 40 NSP tubing is used between els. These parts have a very thick wall thickness so the header will probably
weigh as much as a heavy cast iron manifold. This thickness is necessary with non-stainless tubing
for longevity at the high temperatures encountered. Standard mild steel header tubing will quickly self destruct if used for
a turbo header. These materials have proved to last for several years of hard use on many engines
including road racing applications.
Collector
The collector
is what merges the primary tubes into the turbine inlet. It needs to match the outer circumference of the primary tubes and
the ID at the turbine flange needs to match the hole ID. It is constructed in 4 main parts, made from 1/8 to 3/16 plate stock
which is then welded together. Later, 4 wedges were cut from each corner and 45 degree triangles were added to help match
the tube contours. Alternately, an 8 sided collector can be built or a hammer formed collector made. Hammer forming such thick
plate is very time consuming! For Turbos with round inlet holes, a conical collector needs to be made. This entails cutting
a paper template to simulate the size and shape and lots of cursing and swearing to heat and hammer form into the conical
shape. We recommend that all parts be TIG welded to reduce warp-age. Weld the turbine inlet flange to the collector.
Tube Layout
The turbo should be held in position where it will be mounted. Lots of thought should go into the tube layout to try to maintain
equal lengths if possible and be sure that the tubes clear steering boxes, master cylinders, strut towers etc. It has been
found that actual tube length seems to have little effect on response or power in street applications however, equal lengths
will theoretically give slightly better response. Most of our systems have a 14 to 18 inch primary tube length and this has
worked well.
The 45 and 90 degree els and straight tubing may be duct taped together
to plan the layout. Once you are satisfied with the layout, the tubes may be tacked to the head flange with ONE small tack
on the top. We bolt the flange to a scrap head to aid in tube alignment. Start out from the head flange one piece at a time
working out to-wards the collector.
Once your pipes are all tacked and line up on the collector OK,
carefully bolt the assembly into the car and set the turbo and collector in place. If everything is where you want it, remove
and take it back to the bench. Scribe or mark each tube where it meets the flange and number each tube. Tack each joint in
at least 2 points EXCEPT at the head flange. Now carefully break each tube off of the flange. Weld all the joints completely
on each tube.
Once all the primary tube joints have been welded, they need to
be carefully repositioned as they were before removal from the head flange. Line up your scribe marks and the original tacks.
Tack each tube back in place. The tubes may be moved and twisted slightly to allow the collector ends to meet at the proper
angle and height to align with the collector base. A large hose clamp or vise grips can be used to hold the tubes together.
Once you are satisfied, heavily tack the primaries to the head flange and the ends of the tubes together. Make sure that the
flange is firmly bolted to a scrap head or 1 inch base plate to prevent warp-age. Yes, even 1/2 inch plate will warp.
Center Diamond and Corners
You need to cut and shape corner pieces and a center diamond to plug the holes where the collector meets the primaries. These
should be cut from the 1/8 or 3/16 plate that you used to make the collector. Once satisfied with the fit, weld in place.
You are now ready to weld the collector to the rest of the header.
1/8 X 1 flat stock can be used to brace the edge of the flange to the collector and to the outside of the primaries for extra
strength and longevity.

After ceramic
coating

Coated down pipe and powder coated inter-cooler pipe

T4/T3 hybrid turbo with
H3 compressor, stage 3, .63 exhaust, ceramic coated. A twin port, waste-gate actuator is used for cockpit adjustable boost
via an inexpensive pneumatic regulator.

Complete installation. Note extensive
heat shield to protect master cylinder and brake lines made from aluminum backed Felramic 2000 material.
Section IV
Project:Flathead Starts here!
I hope that helped shed some light on just how Headers are made. The only thing we will
be doing different is the Header Tubing will be much smaller in wall thickness. I have never seen
a Header welded with such thick metal as in the above article. We will be using 1-5/8" mild steel tubing with a
wall thickness of 16 Gauge. The set-up is very similar to the article above, which is why I included it, I was hoping
it would prove useful.
Hopefully you have been following along as we build this
project, if so..you last read how we were building up the Flathead which was just painted back in section III. I cheated
and included a picture from this section to wet your appetite, it was the one where you see one sides finished header and
turbocharger. Believe it or not, I got that side to that state of build, in just a few hours of work (3-4).
On the next side, which will be a mirror image of the first side, I'll go a bit slower and take some pictures as we go.
It was very difficult to take any pictures of the passenger side. I was working alone, and always needed to hold something
or my hands were filthy dirty from the job. Yes ,I wiped all the tubing down with acetone before I started, but
still you get dirty.


The
first picture above is what our J-bend pipes looked like, some times they have a 45° bend in place of the 90° bend.
The second pictures is one of our header flanges. They are water jet cut 3/8" thick steel.
Starting from the begining......I ordered eight (8) 1-5/8" U-Bends and two (2) 1-5/8" J-Bends as a start for the
tubing. We also ordered two (2) 3 into 1 Collectors, and of-coarse all the Turbo-Chargers and their mounting brackets.
The Ford Flathead is unique in that it only has three (3) Exhaust Ports per side, UN-like the usual four (4) Exhaust
Ports on the normal V8 engine. This makes the Headers UN-usual and a little odd looking, but also saves
us fitting and welding on one (1) tube. Before we started any cutting or welding on the Headers, we had to
do alot of thinking and measuring. I tried to conceptualize the Header, with the Turbo-Charger. We needed
to keep the Header up, so it would fit inside the traditional Hot Rod Frame, but not up any more then necessary.
The Header also had to contend with the Turbo-Chargers mounting flange and the SS V-band Clamp, all of
which took up space. Another consideration was the individual Header Tube Length, while I was sure I would
not end up with perfectly equal Tube Lengths, I did want to keep them as close to equal as possible. I don't know
how professional Header builder work, some might use all mathematical formulas, others templates, but I only had
my Imagination. I knew where I wanted the Turbo-Hharger to be, and I knew where I didn't want the tubes
to be, the rest just came as I went along.

This
is a highly polished Stainless Steel exhaust side manifold for the T3-T4 Turbo-charger. These parts look even better
in person, and are what we used on Project:Flathead.

These
are the Exhaust manifold ends for the incoming very hot air of the engine to the Turbo-charger. Again the parts are
highly polished and refined. If compared to the above article, there parts and final header design looks rough to say
the least compared to our parts. Again, if you look around you can fine the nicer stuff, and at very affordable prices.

This
is a 3-into 1 collector, and the same as we used

These
are V-Band Clamps, they are made from Stainless Steel and have highly machined surfaces to seal against.
Before anything got started, I first had to modify all the tubing I had. I started out by cutting all the U-bends in
half, I measured the U-bend section and cut it in half with a band saw. This gave me sixteen (16) short 90° bends
to start work with. To me, the obvious place to start was with one of the out-side Exhaust Ports. I aliened the
Collector with the center of the Engine, and worked by way back from there. Once I had the Collector in place, we could
measure the distance from the first Exhaust Port to the Collector and the distance from the side of the block to the Collector.
With this information, I started cutting some of the short 90° bends to fit. Then just basically re-peated the same
thing for the back Exhaust Port, although there is a slight difference between the two. With these two(2) Ports
fitted, I tach-welded both in place and then had something solid to work off of for the middle Exhaust Port.
This Port was the most challenging, I wanted to keep the tube lengths close, so instead of simply coming out of the engine
and mating up to the Collector with the most direct route, we had to 90° out of the Engine, cross over then under the
first tube and then double 90° back to the Collector. For this section, the J-Bend was just the ticket, I used the
U-Section I saved and three (3) more close 90° short Bends. All in all it turned out pretty good, and I'll promise
to take more pictures when we do the driver side.
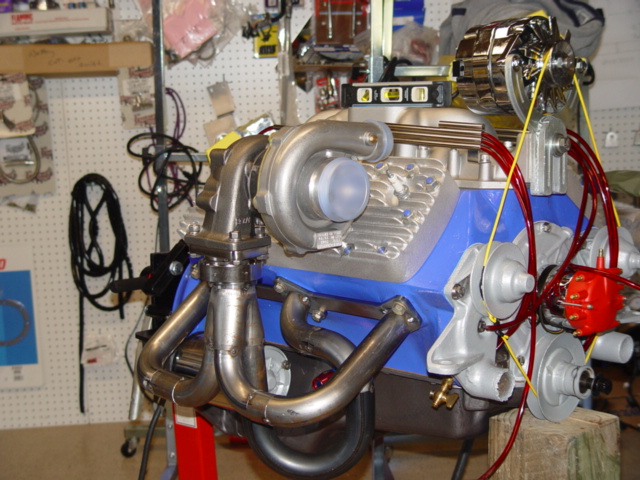



These are the latest pictures of the Flathead. The 6" x 6"
timber is being used to hold the engine level (front to back), this way I can get the exhaust flanges installed and tack welded
in place, while it's level. The goal here, is to try and keep the Turbo-Chargers running as level as possible.
Also, note the bottom row and some of the second row, cylinder head studs. With the new Aluminum heads in-place, these
two rows are noticeably short. They will need to be replaced with longer studs. The Nuts should also have
washers underneath them, to prevent damage to the aluminum heads.
10-06-07
I finally got a chance
to do some much needed work on Project:Flathead. Despite the 90°+
Heat, I managed to get several problems crossed off my "To Do" list.
First up was the Drivers side Exhaust Manifold. Too a certain extent, this was really just
a Mirror Image of the passenger side Manifold we made several days ago. So, with that in mind, I measured all
the pieces on the Passenger side and transferred them to tubbing, and then started with the first Exhaust Port from the front,
just like we did on the other side. I didn't automatically cut any of the pieces, instead I used the marks as a
starting point, and checked if that was a valid or invalid mark. The first port was easy and I even took some pictures
that followed along marking our progress.




Once the first port was tack welded in place, we moved to the rear most
port and duplicated what we did on the first port earlier. What you are looking for here, is alignment. We want
the tubes exiting the ports to be square with the block and level with each other.

The last port was much more difficult, just as it had been on the other
side. But, the learning curve had already been sorted-out by the time we got to this side. I really just needed
an extra set of hands, the measurements were pretty easy, just lining everything up to get the proper fit and angle was the
problem. Once I had a good ideal what was needed at the middle port, I could tach weld the close 90° into position
and then it went much easier. This side took about half the time the prior side took, and that's with me having
to remove everything and start over half way through the process. I'm not sure what was different, but I had several
tach welds burn through, and create two large holes, which is my I scraped everything once and started over. One small
hole or two is repairable, but a series of them isn't.

Here the Exhaust Manifold is finished Tack Welded. The V-Band Clamp was slightly different
then the one we used on the opposite side, so I had to insert a thin section of 2-1/2" SS Tubing between the collars
end and the 4-Bolt Flange.
Once the basic Exhaust Manifold was finished, I re-leveled
the engine and made sure the right and left sides were the same. Same distance off the floor and same angle. The
only hitch in the whole thing was the V-Band Clamps I used on this side were different then those on the other side.
They were identical except for the length of the collar where they attach. For some reason, these were shorter, and
when I welded them to the 4-Bolt flange that attachés the Turbo-Charger to the Exhaust Manifold, that difference in
height made the mounting bolts hit. To compensate for this, I had to break those welds, and insert a small portion of
SS-2-1/2" Tubing between the end of the collar and the 4-bolt flange. This allowed the mounting bolts to now work,
without interfering.
At this point the Exhaust Manifolds or Headers were complete,
so we turned our attention elsewhere. Remember when we first installed the new Elderbrock Aluminum Cylinder Heads
? Well, there were several Head Studs
that were to short, and needed to be fixed. This is where we come into play, I had already ordered the new Head Studs
from Mac's, so now was the perfect time to install them. This is one phase of the project I would have rather skipped,
many because I thought it would be a royal pain. This engine had been sitting around with these head studs in-place
for almost 70 years. And the kicker is the one side sat with the head off for at least 40 years. I could only
imagine how this story would go, and how many head studs I would break off tiring to remove them.
I decided to start on the drivers side, this is the side that sat so long with the head removed, so I though I would tackle
the worst side first. I gave every stud a shot of WD40, and began with the first stud using my 1/2" long breaker
bar and a stud remover. The first one took some effort but it broke free, I turned it about half a turn and gave it
another shot of WD40, then removed it form the block. The second one was about the same and so was the third.
In fact, the whole side came off and although tight, they didn't break off in the block like I had imagined they might.
Wow...this was some really good news, and now I think back and I know why the different Head manufacturers don't mention
that you need to remove the head studs of the lower two rows. They fear it would cost them sales because guys like myself
would fear the removal process. I can certainly see their point, but I do think the right thing to do is to list
all the tools and any modifications needed to install their product. Back to the engine....With the one side now complete
of all the removal, I installed the new studs with a dash of Thread-Locker, and checked that the head would still fit.
It did, so we now turned our attention to the other side.
This was the
protected side, so I was thinking it should go as well or better then the first side did. I really couldn't tell
a difference between the two, they both took the same amount of force, which was plenty. I got all the way down to the
last four (4) studs till I ran into trouble. This came completely unexpected, the stud just broke off. No movement
at all, and the worst part about it was when it broke, I was pulling toward me and the wrench hit me dead center in the eye.
Not on the eye, but in it. Lucky for me I had my hand placed just right where there was only about 1" of wrench
handle sticking out past my hand. Besides not being able to focus for 20-30 minuets, I was fine, but will definitely
wear a shiner for some time. The other remaining head studs came out, just as all the rest had, slow and tough.
True fully, I was lucky, I had but one (1) head stud to repair. If you would have asked me how many I would probably
have before I started, It would have been much more then one (1).
Fixing
a head stud is much like fixing any other broken bolt, it just takes time and patience. The good thing about it, was,
it was easy to get at and in plain sight. I center punched the stud which had broken off just below the deck, and drilled
it out with a 5/16" bit. I tried to remove it with a twist out, but that stud wasn't budging. So, I went
ahead and drilled it out to 3/8" which is the same size you would drill anything to tap a 7/16" thread into.
With a little work, and alot more Patience, I had the old stud removed and the threads back in good shape. All that
was left to do was to install all the new studs and tighten them down, just as we did before. With that part done, I
installed the head and hand started all 48 nuts, 24 per side. Then I got all the nuts hand tight, and torqued them down
on both sides. There are several sites that show head torque values and patterns. Basically you start in the middle
and work your way out from both directions, torquing the nuts to a pre-determined value. I like to take the heads studs
down in three separate torquings, working my way up to the final torque.

This is the passenger side of the engine. If you look close enough, you can see all the new
head studs, they are the ones with the black tops, this side had ten (10) new studs installed. The other side had thirteen
(13) installed.

This shot shows the new head studs and the new nut covers installed. I took this picture, because
it's had to see after the Turbo-Charger is re-installed. Those chrome acorn nut covers sure do shine, and give the
engine a whole new look.
With the Head Studs out of the way, I buttoned-up the Cylinder
Heads and installed all the new chrome nut covers. It's really nice to see all the nuts on, and the covers attached.
Just remember that with these aluminum heads, washers under the nuts are a must have item. The washers help even out
the pressure, and keep the nuts from digging into the softer aluminum heads when tightening. If this would have been
an actual running engine, I would have replaced all the head studs with new, ARP high strength head studs. As it is,
I only used new OEM type studs. Of-coarse, the reason for using the high strength ones is to combat the internal pressures
associated with using Turbo-Chargers or anything that would make Boost. The More Air/Fuel we pack into the Cylinders,
the more Horse-Power we make. The more Horse-Power we make, the more internal stress. The high strength studs are there
to insure the heads maintain a tight seal against the surface of the block. I'm not sure what the real figure is
in regards to added stress, but with the added pressure and more fuel, I would say it's at least doubled.
Now that we have the engine buttoned up once again, I got a chance to snap a few pictures and think about how we want the
Turbo-Chargers to sit. The best I could come up with is what you see here. The two (2) sides are not going to
be the same, they can not be, they are mirror images of each other. What I was able to do, is come up with a scenario
where we can get the two (2) sides as close as possible, a situation that will work. The Turbo-Chargers are clock-able,
meaning they have the ability to rotate on an axis. By loosening the six (6) 3/8" bolts on each compressor (Cold
Side) we can rotate the outlet of each compressor so they match. In this case they will both be pointing up. We
will attach a 90° bend right away, so we can redirect the flow of air to wards the Inter-Cooler. We have made sure
our oil inlet and it's corresponding Outlet are positioned straight up and down, prospectively. This is very important
for good oil flow. Next time I work on Project:Flathead, I'll
mount the oil inlet's and plumb the lines to and from the Turbo-Chargers. We'll use a AN-4 for the feed and
a AN-10 for the return or drain.
I did happen to mount the air filters, I wanted to make sure
there were no issues. For now I'll just leave them on as they protect the Turbo's from dirt and damage.


These last two (2) shots show the engine complete
with it's new Air Filters. I really like the look of them, they give the engine a jet-like look. Plus they
are compact and light weight. With the head studs out of the way, I suppose we will have to turn our attention to the
intake system, and the fuel management portion of the project. Also, it won't be too long till we design the frame
work that will hold everything in place
10-12-07
I haven't been doing to much latley,
but I did manage to get down to the shop today. I mainly did a bunch of stowing supplies, but after that I worked
a little on Project:Flathead. First thing I did, was to make a list of what was now needed. I thought I had some
An-10 Hose, but that was wrong, so on the list it went. The An-10 hose will be used for the Turbo-Charger's oil
drain back into the oil pan. Remember those two oil pan fittings we installed?? That is what they were for.
I also checked to see if we had the supplies to fashion the two oil feed lined to the Turbo-Chargers, and we had everything
but the oil inlet fittings. I was assuming we could simply screw in a 1/8" NPT fitting that converted to An-4,
but that was wrong also. The thread in the turbo body is some sort of Metric thread, so I ordered two oil inlet fittings.
Yes I know, But it is much easier and cheaper to just order the two oil inlet kits then try and find that adapter for the
fitting. If you look, you will not find any metric to AN fittings. So, with those two items out of the way, I
spent a little time visuallizing how the rest of the engine and it's intake system will look. Next time I get the
time, I'm going to start working on that, and se if we can't get something going. eally the rest of the project
depends on that key area.